Introduction
Zamac caps are widely used in various industries due to their durability, aesthetic appeal, and versatile applications. These caps are made from Zamac, a family of alloys with a base composition of zinc, aluminum, magnesium, and copper. They are often found in cosmetic packaging, particularly as Zamac perfume caps, due to their ability to convey a sense of luxury and refinement.
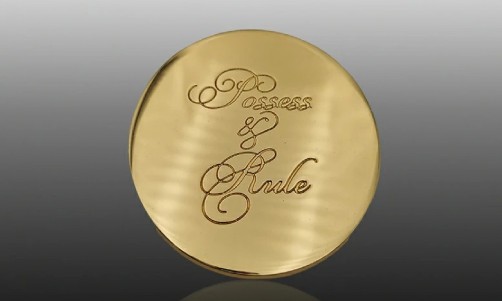
Importance of Surface Finish in Zamac Caps
The surface finish of Zamac caps is crucial for both functional and aesthetic reasons. A polished surface enhances the visual appeal, making the product more attractive. A smooth, polished finish can also provide functional benefits, such as improved corrosion resistance and easier maintenance.
What is Polishing?
Definition of Polishing
Polishing is a process that involves smoothing and shining a surface to enhance its appearance and functionality. It can be achieved through various methods, including mechanical polishing, chemical polishing, and electrochemical polishing. Each technique has specific applications and benefits, depending on the desired outcome and the polished material.
Materials and Tools Used
The polishing process for Zamac caps involves using specific tools and materials to achieve the desired finish. Standard tools include polishing wheels, buffing pads, and abrasive compounds. The workflow typically starts with a coarse polish to remove imperfections and gradually moves to finer polishes to achieve a smooth and shiny surface.
Benefits of Polishing Zamac Caps
Aesthetic Enhancement
One primary reason for polishing Zamac caps is to improve their aesthetic appeal. A polished Zamac cap looks more attractive and can significantly enhance the product’s perceived value. For instance, Zamac perfume caps polished to a high gloss finish can make the packaging look more luxurious and appealing to consumers. Polishing also allows customizable finishes, such as matte, glossy, or satin, to suit different design preferences.
Functional Improvements
Polishing Zamac caps also provides several functional benefits. A polished surface is smoother, which can reduce friction and make the caps easier to handle and use. Furthermore, the polishing process can improve the corrosion resistance of Zamac caps, protecting them from environmental factors that could cause deterioration. This is particularly important for Zamac perfume caps, which must maintain their appearance and functionality over time.
Durability and Longevity
Polished Zamac caps are more durable and can withstand wear and tear better than unpolished ones. The polishing process creates a protective layer on the caps’ surface, enhancing their resistance to scratches and other damage. This increased durability ensures that the caps maintain their aesthetic and functional qualities for extended periods, providing better value for consumers.
The Polishing Process for Zamac Caps
Initial Inspection and Cleaning
The polishing process begins with an initial inspection and cleaning of the Zamac caps. Starting with a clean surface is essential to ensure the polishing is effective. Any dirt, grease, or other contaminants can interfere with polishing and result in a subpar finish. Cleaning methods may include ultrasonic cleaning, degreasing, and rinsing to prepare the caps for polishing.
Rough Polishing
Rough polishing is the first step in the actual polishing process. This step involves using coarse abrasives to remove surface imperfections, such as scratches or casting marks, from the Zamac caps. The goal is to create a smooth base that can be further refined in subsequent steps. Rough polishing typically uses abrasive wheels or belts with a coarse grit.
Fine Polishing
Fine polishing follows rough polishing and involves using finer abrasives to achieve the desired finish. This step is crucial for achieving the high shine and smoothness often required for Zamac caps, especially Zamac perfume caps. Fine polishing can be done using polishing wheels with finer grits and various polishing compounds designed to enhance the surface finish.
The Polishing Process for Zamac Caps
Final Inspection and Quality Control
After the delicate polishing stage, a final inspection and quality control process is crucial. This step ensures that the Zamac caps meet the required standards and specifications. The inspection process typically involves:
- Checking for any remaining imperfections.
- Verifying the smoothness and consistency of the finish.
- Ensuring that the caps meet aesthetic standards.
High-quality Zamac caps manufacturers often have stringent quality control procedures to guarantee that their products are flawless and ready for the market.
Challenges in Polishing Zamac Caps
Material Properties of Zamac
Zamac’s composition presents specific challenges during the polishing process. The alloy’s zinc content can make it more susceptible to over-polishing, leading to material loss and structural weakening. Additionally, the varying hardness of the metals in Zamac can result in uneven polishing if not carefully managed. Understanding these material properties is essential for achieving a high-quality finish without compromising the integrity of the caps.
Avoiding Over-Polishing
Over-polishing is a common risk when working with Zamac caps. Excessive polishing can thin the material, weaken the caps, and create uneven or wavy surfaces. To avoid over-polishing, using the right amount of pressure and choosing appropriate polishing compounds is crucial. Experienced Zamac caps manufacturers are skilled at striking the perfect balance between achieving a high-quality finish and maintaining the caps’ structural integrity.
Alternatives to Polishing
Coating and Plating
In some cases, coating and plating can serve as alternatives to polishing. These methods involve applying a layer of another material, such as chrome, nickel, or paint, to the surface of the Zamac caps. Coating and plating can provide similar aesthetic and protective benefits as polishing but with additional options for color and texture. However, these methods can also add to the production cost and may require further processing steps.
Anodizing and Other Surface Treatments
Other surface treatments, such as anodizing, can also be considered alternatives to polishing. Anodizing creates a protective oxide layer on the surface of the Zamac caps, enhancing their corrosion resistance and durability. This process can also add color and improve the caps’ aesthetic appeal. These alternative treatments might be preferred over traditional polishing methods depending on the specific requirements.
Conclusion
Polishing is necessary for Zamac caps due to its significant impact on aesthetics and functionality. The polishing process enhances the visual appeal, making the products more attractive to consumers, especially in industries where presentation is crucial, such as with Zamac perfume caps. Additionally, polishing improves the durability, corrosion resistance, and overall longevity of the caps, providing better value and performance.